The Future of Plastic Shot Molding: Developments and patterns to See
As the plastic injection molding industry advances, numerous crucial fads are emerging that pledge to improve its landscape. Automation and clever manufacturing techniques are established to boost efficiency, while the shift towards sustainable materials reflects an expanding ecological awareness.
Automation and Smart Production
As the plastic injection molding sector evolves, automation and clever manufacturing are taking center phase, revolutionizing manufacturing procedures - Plastic Injection Molding. The combination of innovative innovations such as robotics, IoT (Net of Things), and man-made knowledge is allowing suppliers to enhance efficiency, minimize operational costs, and improve item quality. Automated systems improve workflows, minimizing manual treatment and boosting throughput, which is important in meeting the climbing demand for fast production cycles
Smart manufacturing modern technologies help with real-time monitoring and information evaluation, permitting firms to maximize device efficiency and predict upkeep demands. This proactive technique not only decreases downtime however additionally extends the life expectancy of tools. The use of collaborative robotics, or cobots, improves the flexibility of production lines, allowing devices and workers to operate side by side securely and effectively.
The adoption of automation in plastic injection molding is not just a pattern however a critical imperative for services aiming to stay competitive in a global market. By harnessing these innovations, makers can attain greater accuracy, minimize waste, and adjust promptly to transforming consumer needs, positioning themselves for lasting growth in a progressively automatic future.
Sustainable Materials and Practices
The push towards automation and wise manufacturing has led the way for a better focus on lasting products and techniques within the plastic shot molding sector. Business are progressively seeking eco-friendly choices to typical petroleum-based plastics, causing the adoption of bio-based and recycled materials. These lasting products not only reduce ecological effect however also straighten with customer demand for greener items.

Moreover, cooperation in between suppliers, product distributors, and ecological companies is cultivating innovation in the advancement of lasting materials that meet efficiency criteria without endangering quality. As regulations around plastic use end up being more stringent, the industry is positioned to adjust by accepting these lasting techniques, making sure long-lasting practicality and reducing reliance on non-renewable sources. The integration of sustainability into plastic injection molding is not simply a trend; it is becoming a necessary element of company duty and functional excellence.
Breakthroughs in 3D Printing
Current improvements in 3D printing modern technology are dramatically changing the landscape of plastic shot molding. As soon as challenging or impossible to attain via typical techniques, the assimilation of additive manufacturing processes permits for the fast prototyping of complex geometries that were. This capacity not only speeds up item growth cycles yet likewise reduces material waste, aligning with the expanding need for lasting production practices
Additionally, the appearance of crossbreed production methods, which incorporate 3D printing and injection molding, uses manufacturers the capability to create complex layouts while preserving the performance of automation. This method makes it possible for the production of personalized components customized to specific consumer requirements without compromising the rate and scalability that injection molding offers.
Furthermore, innovations in materials, such as high-performance polymers and composites particularly made for 3D printing, are improving the functional capabilities of printed elements. These products can hold up against greater tension and display boosted thermal residential or commercial properties, making them appropriate for even more requiring applications.
As 3D printing proceeds to evolve, its integration into plastic injection molding processes guarantees to improve productivity, minimize expenses, and foster advancement in item layout, placing suppliers to much better fulfill the obstacles of an affordable market.
Information Analytics and IoT Assimilation
Information analytics and the assimilation of the Net of Points (IoT) are changing plastic shot molding by supplying makers with unmatched understandings into their operations. By leveraging real-time data accumulated from interconnected equipments and sensors, manufacturers can monitor performance metrics, recognize inadequacies, and enhance production processes. This data-driven strategy promotes anticipating maintenance, reducing downtime and discover this info here extending tools life-span.
Moreover, IoT integration allows for boosted high quality control. By continuously tracking variables such as cycle, pressure, and temperature times, suppliers can quickly spot deviations from developed criteria and make adjustments in real time. This not just enhances item consistency but additionally decreases waste and scrap prices.
The fusion of data analytics and IoT innovations likewise encourages makers to take on more dexterous production strategies. With access to thorough information analytics, companies can react to market needs with better adaptability, changing manufacturing routines and configurations as required. This versatility is vital in a rapidly altering production landscape.
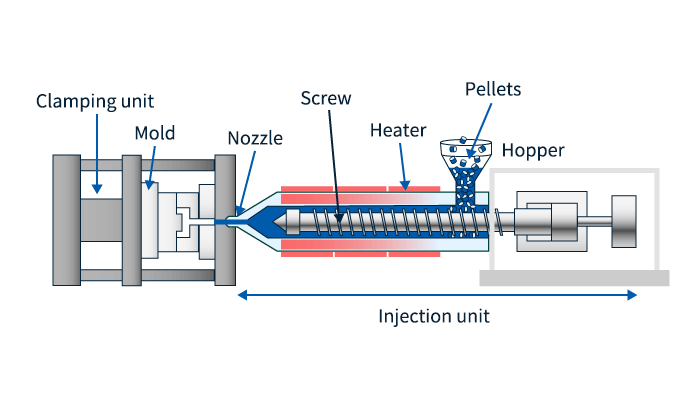
Personalization and Layout Adaptability
Just how can personalization and design adaptability improve the competitiveness of plastic shot molding? Personalization allows suppliers to fulfill particular client demands, accommodating one-of-a-kind her response measurements, shapes, and capabilities that conventional products might not fulfill.
Innovations in style technologies, such as computer-aided layout (CAD) and rapid prototyping, more reinforce this fad. These tools make it possible for designers to develop elaborate patterns and intricate geometries, which can be flawlessly integrated right into the production procedure. Consequently, makers can react swiftly to transforming consumer preferences and market needs.
Furthermore, the execution of modular tooling systems enhances style adaptability, permitting quicker adjustments between different item layouts without click this link comprehensive downtime. This flexibility can lead to decreased preparations and reduced production prices, making companies much more competitive and active. Inevitably, embracing customization and style adaptability in plastic shot molding not only raises item offerings yet also strengthens market positioning in an ever-evolving landscape.
Final Thought
The future of plastic shot molding is identified by considerable improvements in automation, sustainable techniques, and cutting-edge products. Personalization through modular tooling and rapid prototyping will certainly allow makers to remain competitive and receptive to the vibrant needs of the market.
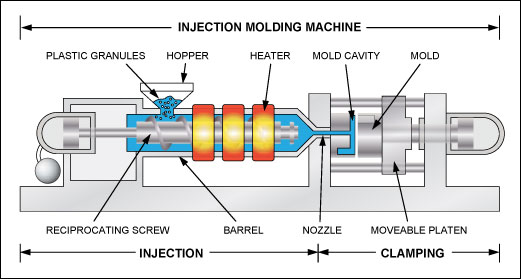
The future of plastic injection molding is characterized by significant improvements in automation, sustainable techniques, and ingenious materials.